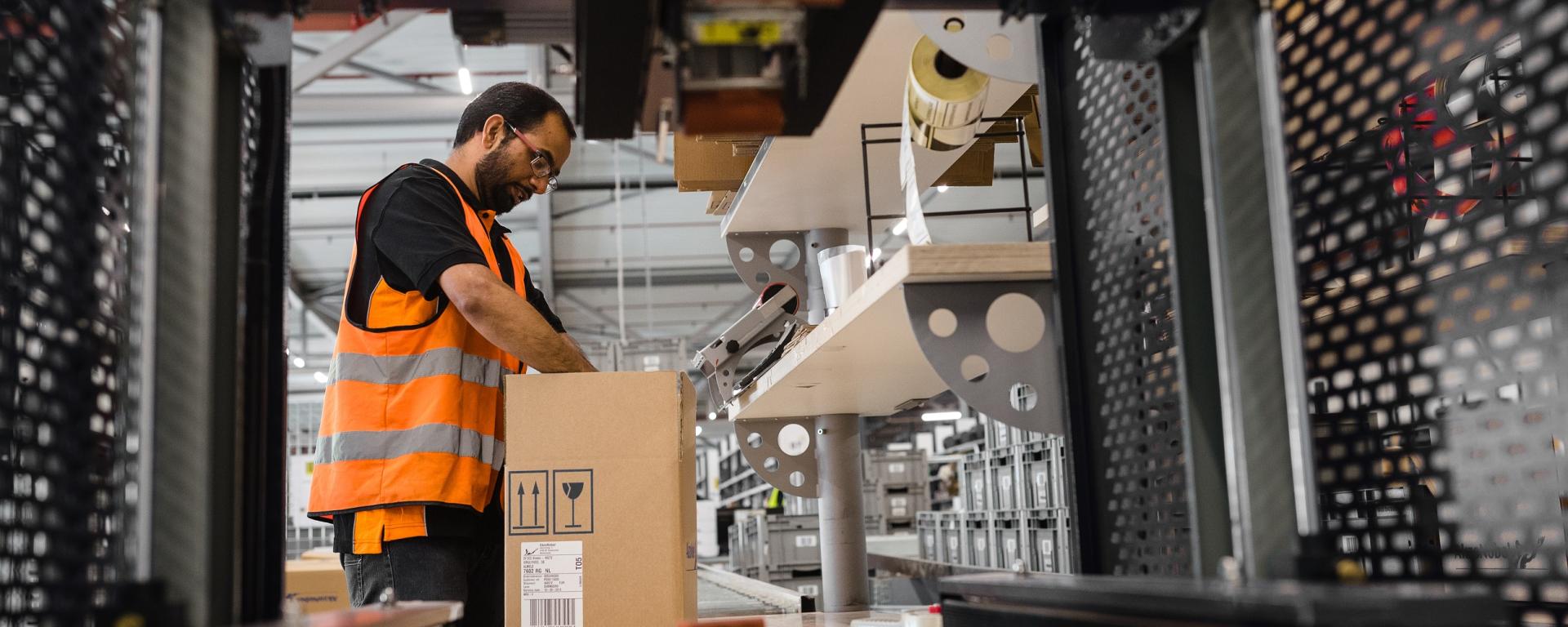
Kinto is a global supplier of high-end tableware, drinkware and interior accessories. Based in their office in Amsterdam, they operate in the European market through wholesalers and directly with consumers.
High-end
A large part of Kinto’s products are made of glass, ceramics and porcelain –all highly fragile materials which must be treated with great care. Since 2017, Kinto has been working with Vos Logistics to carry out various logistics activities for their products.
Warehousing and e-fulfilment
Kinto’s original logistics challenge was twofold: warehousing products and distributing to its customers in Europe; a customer base which consists mainly of major retailers and wholesalers with correlating delivery procedures.
Since the beginning of 2019, Kinto has had its own webshop which means it can serve its customers directly with a wider product portfolio. This development is in line with Kinto's growth strategy in Europe and corresponds well with the logistics services of Vos Logistics. To support Kinto in their challenge and optimize operations as much as possible, Vos Logistics has succeeded in providing for both requirements under one roof. This has the following benefits:
- A single point of storage
- No inefficient replenishment transports between two locations
- Enabling Kinto to further grow their sales without any hassle.
It is Kinto’s mission to constantly develop high-end products which balance usability and aesthetics. With a range that covers tableware, drinkware and interior items, their collections are created with the aim of suggesting a thoughtful, comfortable lifestyle. Kinto values simplicity and subtle elegance; their products are designed to integrate harmoniously in the surrounding space while adding their own unique touch. Kinto believes in products which are easy to use on a daily basis; human activity such as holding, pouring, and drinking are carefully considered in design details.
Product packaging
One of the challenges faced in the beginning of our partnership was to safely transport products to customers, bearing in mind that these products are highly fragile and transported via parcel network. Together with Kinto, we explored a variety of different packaging options and cushioning materials. As a result, we have significantly reduced breakages and increased overall delivery performance; all achieved by using thicker carton (reducing impact during transport) and switching from air pillows to recyclable packaging paper (reducing internal movement).
“Vos Logistics is able to offer both, conventional warehousing and a compact e-fulfilment operation in one state-of-the-art facility in Oss, the Netherlands. Ranging from pallet shipments via our international fleet to daily pickups by our strategically selected parcel carriers with delivery networks throughout Europe. Combining these two different operations, both managed by a single point of contact, enables us to optimize and simplify our clients’ logistics.’’ Marcel van Etten, Business Development Manager Solutions.
System integration
With the growth of logistics activities and the increasing number of online orders, Kinto and Vos Logistics are working behind the scenes on an online shop integration process. By linking the online shopping platform with the Warehouse Management System (WMS), a complete digital dataflow is created, which reduces errors in data entered manually. This is a development in line with our policy of continuous improvement of logistics processes.
A challenge?
Get in touch.
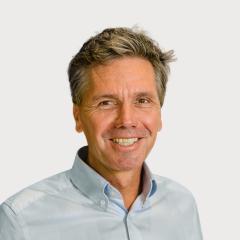