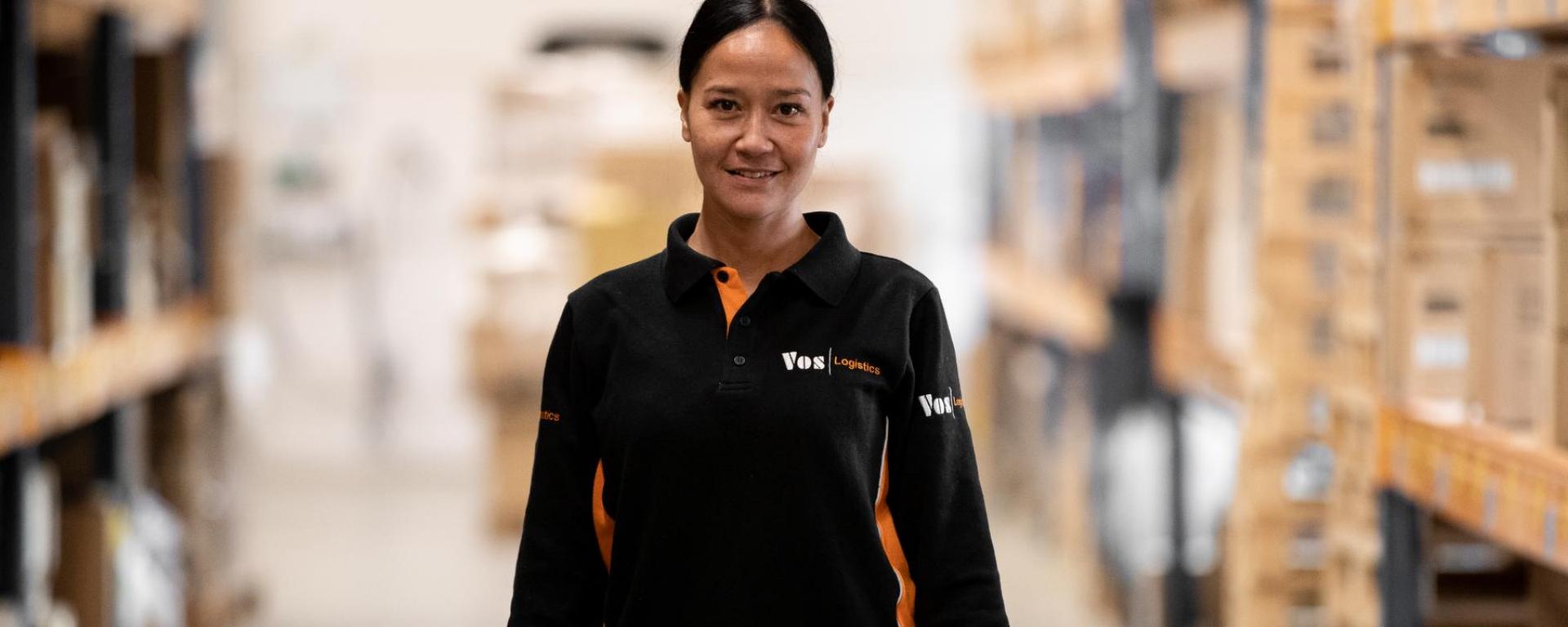
Labor market
In 2020, the pandemic required more focus on the safety of our staff than ever. When the pandemic arrived in March, we acted quickly to modify work processes and establish protocols to ensure our people remained safe. We updated our staff regularly about the virus, the consequences of government decisions and the implications of these decisions on their respective jobs
Training and development
In 2020, we kept our safety standards high and continued to conduct digital training as well as on-site training, combining classroom learning with hands-on practical training. Training sessions dropped from 3,268 in 2019 to 2,029 in 2020. Total training hours were reduced by around 30%, from 28,943 in 2019 to 19,933 in 2020. The reasons behind the reduction in training hours were primarily pandemic related: we hired fewer international drivers and there were fewer opportunities for physical attendance.
Safety
As people adhered closely to the distancing measures, there were fewer accidents. Accordingly, the lost time injury rate dropped from 0.68 in 2019 to 0.62 in 2020. In addition, we have kept our eyes on the latest and safest material handling equipment available and will install new equipment with an even higher safety rating in our warehouses in 2021.
Health
As the pandemic restrictions required people to stay at home and get tested if they showed any symptoms, there was an increase in the sick leave rate. Absence due to illness rose to 4.37%, up from 3.18% in 2019. The sick leave rate increased substantially in 2020, with a peak in March. Although we do not know the extent to which the sick leave rate can be attributed to the pandemic, there is a strong chance that it was related. A fair comparison to 2019 – which was not influenced by the pandemic – is therefore not possible.